Commercial Lean Construction Services in Houston, TX
How do you build a 14-story tower and parking garage from ground-breaking to tenant move-in in 364 days?
Anslow-Bryant utilizes Lean Construction as a core principle in every aspect of our work. Lean Method brings added value by eliminating waste. Our Lean Construction principles look to maximize workflow by eliminating waste; workers waiting on work or work waiting on workers.
Lean Construction in Commercial Markets
Lean Construction processes will transform your project’s delivery. As an Anslow-Bryant partner, you’ll receive customer-focused services that aim to optimize your project resources. The Anslow-Bryant Lean Method focuses on the elimination of waste. The 8 forms of waste are:
- Over-production
- Transportation
- Excess inventory
- Defects
- Over-processing
- Wasted motion
- Waiting time
- Wasted potential
A core tenant of the Anslow-Bryant Lean Method is Continuous Improvement. We are always looking for opportunities to increase value and eliminate waste at all steps of the building process and from all team members. Buy-in from all parties is essential to the Lean process; we hold Daily Huddles with all of our trade partners on-site to discuss the day’s activities, and ensure we have no unanticipated interruptions to the project. Lean at it’s core is simple: find things that bug you, and fix them.
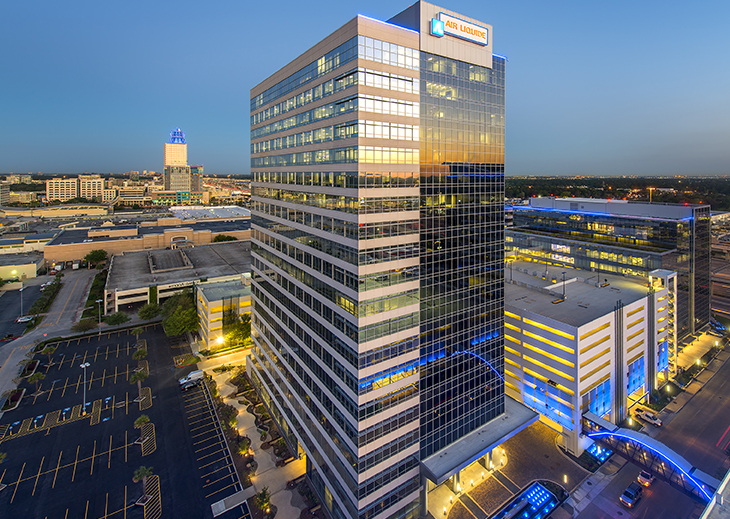
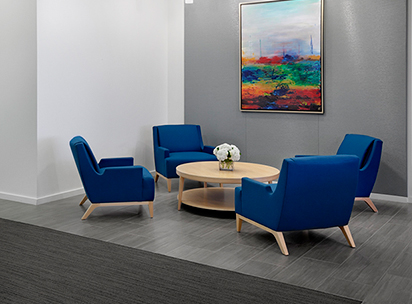
Lean Construction at Anslow-Bryant
Anslow-Bryant utilizes Lean Construction principles and in particular the “Last Planner” methodology in our on-site schedule management. This brings added value by cutting out wasted material, wasted time, time delays, and cluttered job sites. Our Lean Construction program maximizes work flow, minimizes labor and material waste due to re-work from out of sequence operations and maximizes off-site fabrication to minimize on-site storage.
Lean is about developing principles that are right for your organization and diligently practicing them to achieve high performance that continues to add value to the customers and society.
The Anslow-Bryant Advantage
We don’t pursue projects — we pursue relationships. At Anslow-Bryant, you’ll partner with an engaged and responsive team who shares your values. You can expect innovative approaches to your project, including Lean Construction techniques, and an uncompromising commitment to safety initiatives. Rest assured that every Anslow-Bryant staff member has OSHA and site-specific training to help make your final build safer.
Partner With Us
Learn what we can do for you. Discover how our Lean Construction principles can benefit your Houston-area business by contacting us online today.